DÉCOUVREZ LES SECRETS DE FABRICATION DU CORDAGE DE TENNIS
Ne vous êtes vous jamais demandé comment était fabriqué le cordage de tennis et de squash ?
Suivez le guide !
ETAPE 1 : CRÉATION DU CORDAGE
Pour s’intéresser à la fabrication du cordage, il faut d’abord remonter à sa conceptualisation.
Cette étape nécessite une analyse approfondie et complexe : comprendre les besoins des joueurs pour trouver le produit qui les aidera à améliorer leur niveau de performance ou le confort de jeu.
Ainsi, lorsque Tecnifibre a inventé, en 1983, une nouvelle technologie unique, le polyuréthane, elle révolutionne ainsi le marché. Les cordages "TGV", "NRG²", ou "X-One", sont construits autour d'un cœur constitué de fibres synthétiques immergées dans du polyuréthane.
C’est notamment pour se rapprocher des cordages en boyau que ces cordages ont vu le jour : un assemblage de fibres de différents matériaux tels que le polyamide ou le polyester est enveloppé avec un manteau plus résistant.
L’objectif : offrir aux joueurs d’avantage de confort et jouabilité, à l’inverse du polyester, beaucoup plus rigide et source de blessures aux bras et à l’épaule pour les joueurs.
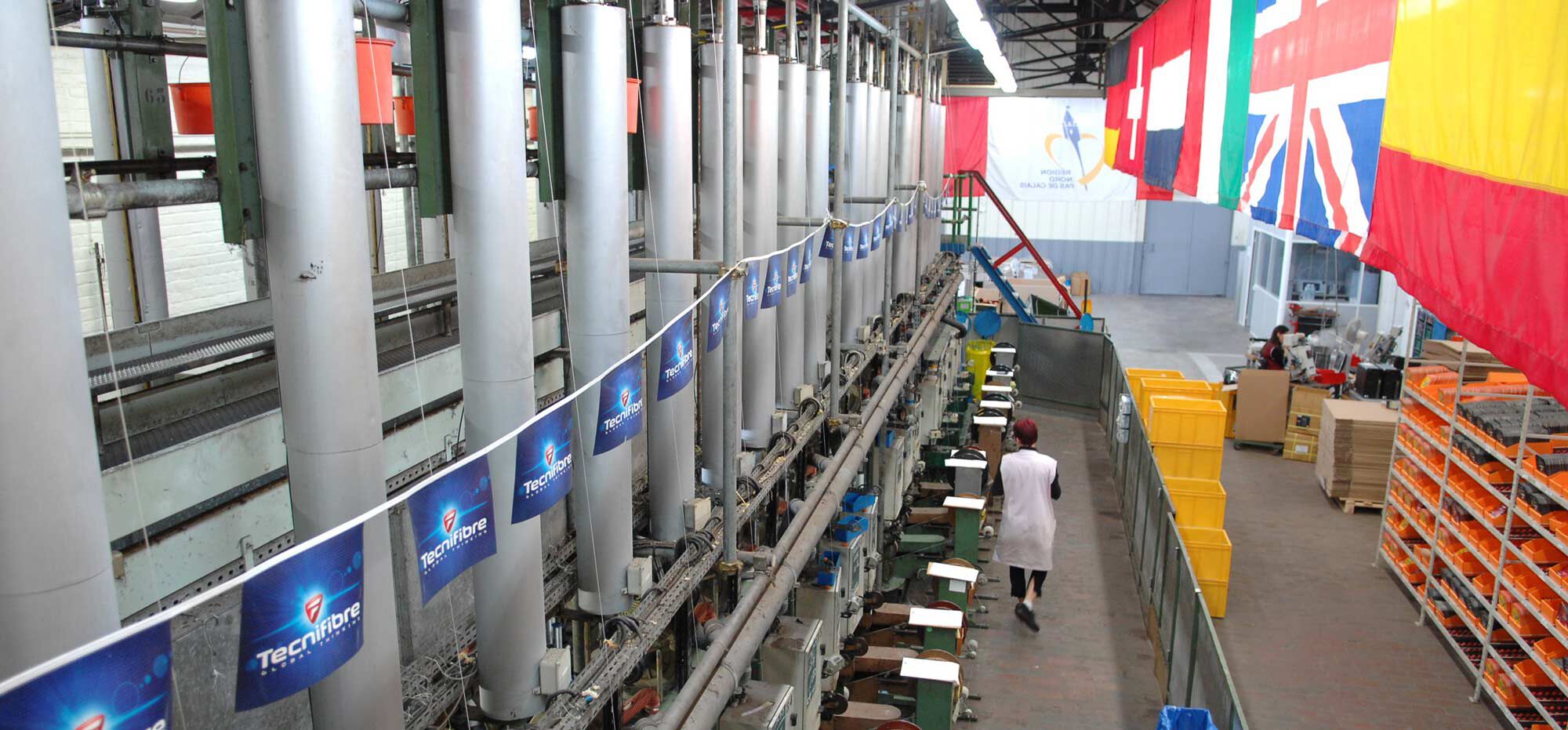
ETAPE 2: FABRICATION DU CORDAGE
Une fois le concept défini, la phase de fabrication débute.
Il convient dès lors de rentrer dans les considérations techniques, pour imaginer les matériaux nécessaires et le processus d’assemblage.
Dans le cas de Tecnifibre, c’est l’usine Cousin Frères, issue d’une longue tradition industrielle de la fileterie, qui fabrique des cordages 100% made in France. Leader sur le segment des multifilaments, l’usine met en place les processus de fabrication en suivant un cahier des charges précis.
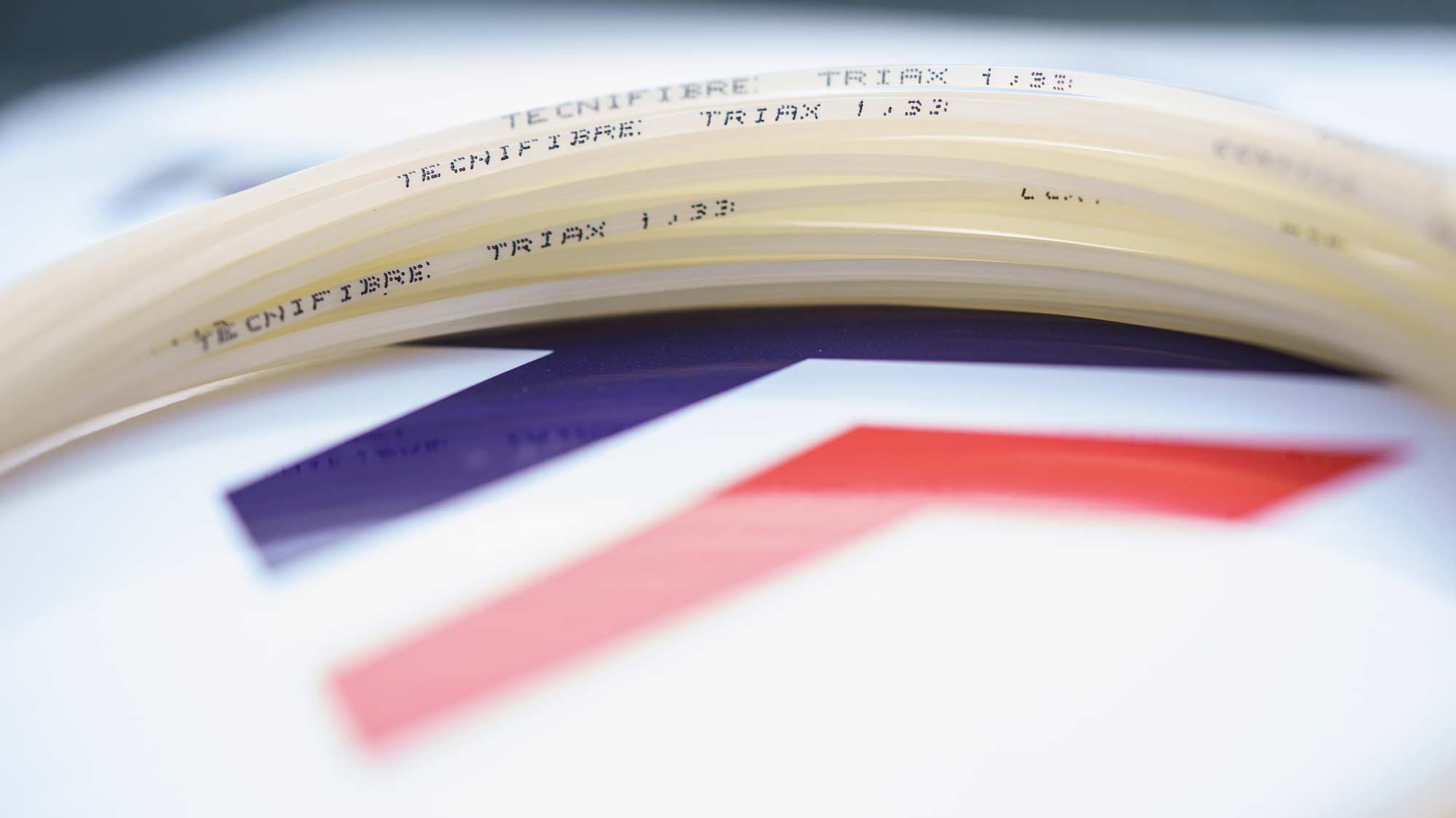
Les matières premières sont le fil et le polyuréthane. Le fil est livré en grandes bobines dont l’usine consomme plus de 20 tonnes par an. Puis chaque fil est imprégné individuellement par les machines de résine de polyuréthane, à base de solvant. Il est possible de mixer les fibres dans la corde (polyamid/polyester), colorer la résine ou encore jouer sur la torsion de la corde et la tension des fils.
Les étapes clés ? L’élimination du solvant, la fusion du polyuréthane et le lissage.
Les facteurs clés sont la matière première, la température, la vitesse de production et le nombre de tours au mètre que l’on met dans les cordages (…).
"Je pense qu’il y a un réel savoir-faire. On a toujours souhaité garder la mainmise sur la production. On a beaucoup de confrères qui ont externalisé dans des pays lointains ; chez Tecnifibre, on continue même à conditionner nos produits sur place"
Jean-Christophe François
Responsable de la production
ETAPE 3 : TEST ET MISE SUR LE MARCHÉ
Une fois le cordage créé, vient l’heure capitale des tests grandeur nature.
L’échantillon est alors ajusté pour correspondre aux besoins des joueurs et à la charte de qualité de la marque.
Pour cela, sont organisés des tests réalisés en externe. Pour les sensations en jeu, ils sont notamment testés par un ancien joueur professionnel dont la mission est de pousser le cordage à sa limite. Des frappes, et encore des frappes.
Ces tests sont supervisés par des vérifications techniques en laboratoire.
« Les tests dynamiques nous permettent d’avoir une idée de la réponse dynamique d’un cordage une fois posé sur une raquette » explique Frédéric Salomon, ingénieur R&D
Lorsque toutes les parties se sont mises d’accord et que le produit est parfaitement calibré, vient alors l’heure véridique de la mise en marché.
Pour offrir aux joueurs le meilleur !
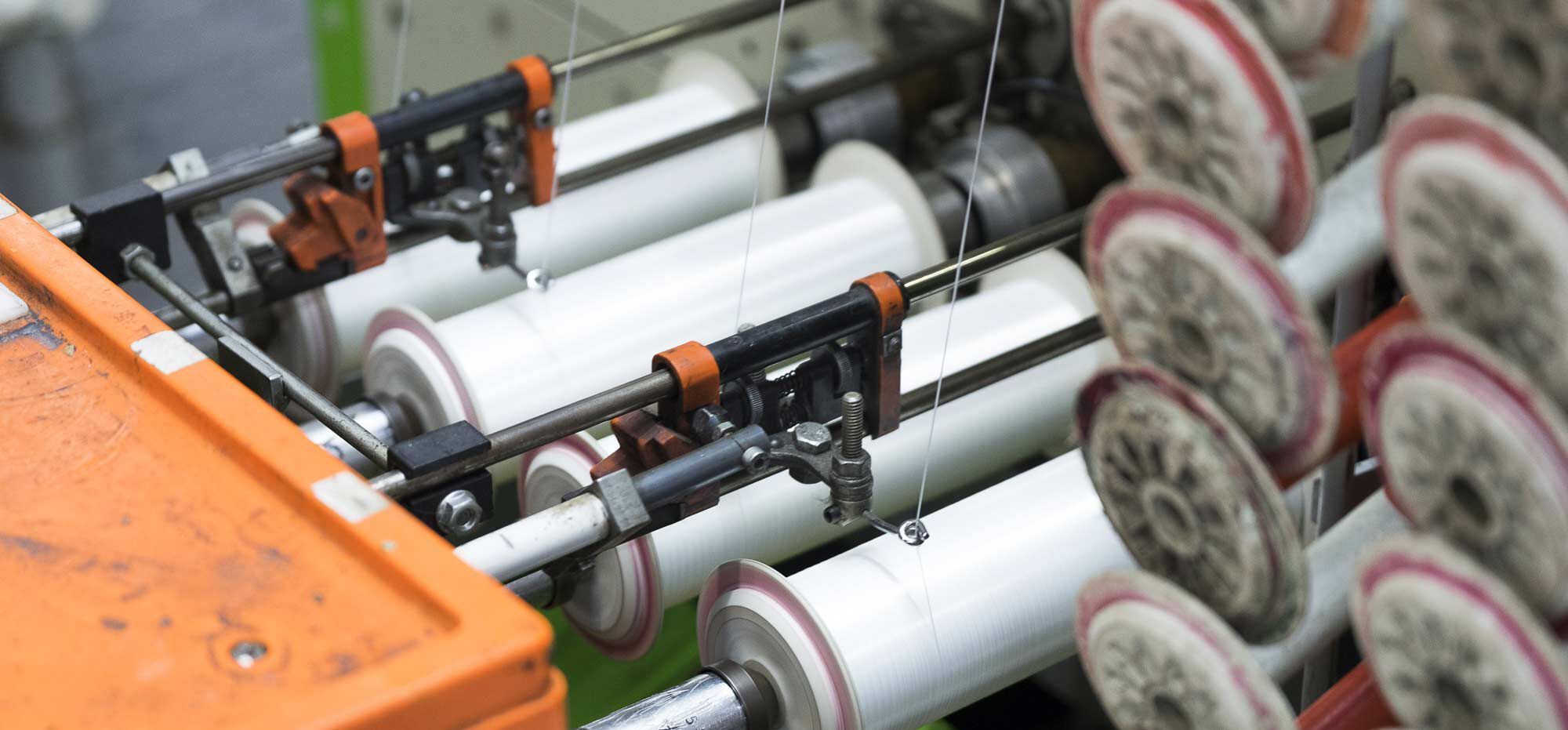